The company Smart Motor Devices has assigned and successfully solved the task - to develop and offer to the industrial market a device for controlling DC brushless motors - simple and not expensive like most BLDC controllers, but solving complex motion problems - in order to rid the system of expensive and complex PLCs. Such a device is BLSD‑20Modbus - a programmable device for controlling three‑phase brushless motors.
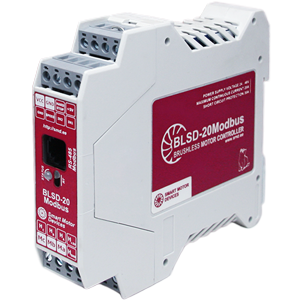
Brushless motors are one of the most common types of electric drives in industry, with which both positioning and speed control can be implemented. This is an effective, simple and inexpensive way to solve a wide range of tasks. However, even with a slight complication of the operating algorithm, there is a need to use additional devices - motion controller or PLC, which take over this function. Such additional devices increase the cost of the drive, require specialized knowledge of setup and programming from the user, and also increase the time until the end device is put into operation.
Smart Motor Devices follows the principle of improving functionality without complicating or increasing the cost of the device. To work with brushless motors, we offer a programmable controller that combines motor control and the main functions of a PLC - analyzing the states of external inputs and programming movement. A customer doesn't need to be a specialist to program the controller - the process is simple, and the development environment is provided free of charge.
For which motors? For 3‑phase DC brushless motors with Hall sensors up to 1000W.
In order not to complicate the system and make it as simple as possible to use and at the same time reliable and trouble‑free without increasing the cost of the final device, the developers of Smart Motor Devices follow a simple principle - for each type and power of the motor there is its own controller model.
In this review, we present a programmable controller designed specifically for three‑phase DC brushless motors with Hall sensors, with voltages from 24 V to 48 V, power up to 1000 W.
Key features and functionality
- Speed control;
- Position control;
- Autonomous operation according to a program recorded in memory;
- Quick and easy programming of the operating algorithm using the provided software;
- Data exchange via Modbus when working on an RS‑485 network;
- Smooth, adjustable acceleration and stopping;
- Limiting the maximum current and output torque of the motor to protect both the motor itself and the surrounding mechanics;
- Safety circuit and HARD_STOP signal for quickly stopping and de‑energizing the motor in case of an emergency;
- Additional programmable discrete inputs for coordination with external devices;
- Analog input, which can be used to control speed or position, or for other purposes.
Programming BLSD‑20Modbus controllers
BLSD‑20Modbus controllers can operate both as a slave in the RS‑485 Modbus network, and autonomously using a program recorded in its memory. Both options provide the ability to program, store the operating algorithm in non‑volatile memory and execute this algorithm.
To configure, program, and also monitor the current operation parameters of the drive, it is convenient to use the special software - Modbus Special Utility program, which is supplied freely for working with the controller.
To create custom programs, the simplest possible command system is proposed, which allows the customer to compose motor control algorithms in the form of a sequence of executed instructions. The program can use loops, wait timers, conditional and unconditional, relative and absolute jumps, mathematical operations, and supports working with subroutines. The maximum program length is 1024 instructions. To work with data, store intermediate information and organize conditional transitions, 10 system registers are provided.
The command system includes the following types of instructions:
- Instructions for controlling the movement of the motor (including speed control, relative or absolute positioning, tracking mode);
- Instructions for setting or changing motion parameters;
- Instructions for analyzing the states of external discrete inputs;
- Instructions and registers for reading the value of an analog input;
- Instructions to write a value to a register. 16‑bit and 32‑bit operations are available;
- Comparison and conditional jump commands allow to implement program branches;
- Unconditional jump instructions allow to unconditionally jump to a specific program instruction;
- To shorten the algorithm and simplify the program code, instructions are provided for calling subroutines;
- Instructions for organizing cycles - cyclic execution of a sequence of commands;
- Instructions for organizing a temporary delay;
- Mathematical operations addition, subtraction, division and multiplication;
- Logical operations;
- Shift operations.
Final result
The combined functionality of the controller - basic functions for motor control and program mode( that allows processing and converting data during operation) - determines wide possibilities for using the drive. When installing BLSD‑20Modbus controllers into the end device, in many cases it is possible to avoid using of complex and expensive PLCs, since the controller independently implements all the necessary functionality.
As a result, Smart Motor Devices offers excellent models to control BLDC motors, which are:
- cost‑effective;
- user friendly and easy to use;
- full‑functional for motion control;
- equipped with protection and a reliable device;
- realizes complex motion algorithms without using a PLC.