Articles
This section publishes articles and technical materials on electric motors and their control.
Articles
This section publishes articles and technical materials on electric motors and their control.
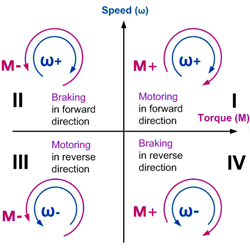
Four‑quadrant DC motor operation
The article describes the concept of four‑quadrant operation of a DC motor – motoring and braking modes, and considers the speed and torque vectors for four variants of motor operation.
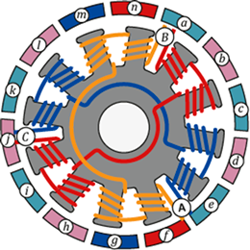
Basics about BLDC motors
The article describes in detail the operating principle of a brushless motor, provides an example of the phases switching sequence and calculation of rotor positions for a full 6‑stage switching cycle.
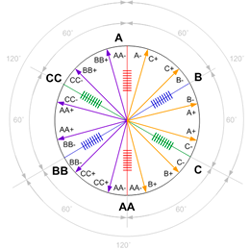
DC Brushless motors control
The longread article provides a detailed analysis of DC brushless motor control: examples of commutation - directions and force vectors for motors with different numbers of poles, determining the rotor position using BEMF and Hall sensors.
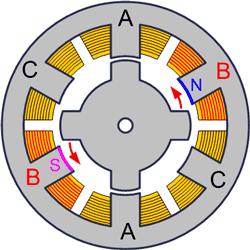
Stepper motor types – VR, PM and hybrid motors
The implementation of the design of stepper motors can be divided into three versions: variable reluctance (VR) stepper motors, permanent magnet (PM) stepper motors and hybrid stepper motors. These types are different in some performance characteristics.
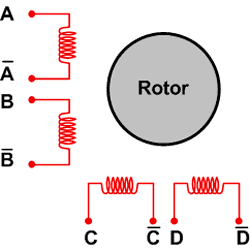
Bipolar and unipolar stepper motors
Strictly speaking, it is more correct to say that it is not the stepper motor itself that is bipolar or unipolar, but its connection to the control driver. Some motors have one winding in each phase, which must be reversed by the driver to change the direction of the magnetic field. This type of motor requires a bridge driver, or a half‑bridge driver with bipolar power supply.
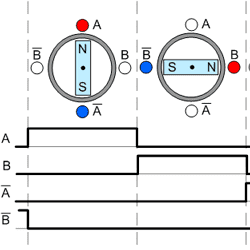
Full‑step stepper motor phase control
The full‑step operating mode of a stepper motor can be implemented in two ways. The first control method is provided by alternating phase switching. This method is called «one‑phase‑on» full step or wave drive mode. The second method is with phase overlap control: two phases are switched on at the same time. It is called «two‑phase‑on» full step or simply full step mode.
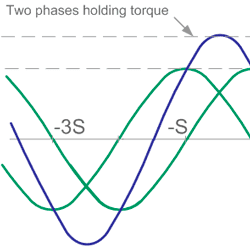
Half‑step stepper motor phase control
Half‑step mode is a step‑by‑step combination of «one and two‑phase‑on», when the rotor moves a half of the main step. This control method is quite common since a less step angle stepper motor costs more and it is good advantage to get 400 steps per revolution instead of 200 from the same motor.
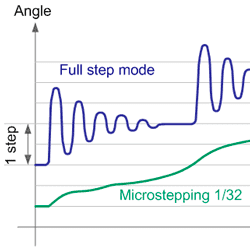
Microstepping operation of stepper motors – principle, output torque and motion precision
Microstepping operation mode of stepper motors can be achieved by creating a magnetic field that rotates more smoothly than in full or half‑stepping modes. The result is less vibration and near‑silent operation even at speeds close to zero. In addition, a smaller step angle can provide more accurate positioning.
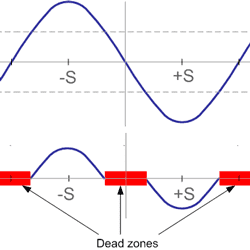
Stepper motor operation - dependence of torque on speed, influence of load
The torque produced by a stepper motor depends on the speed, winding current, and driver circuit. For an ideal stepper motor, this dependency is sinusoidal.
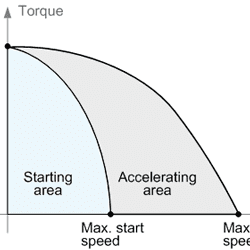
Stepper motor acceleration
In order to operate at high speed from the acceleration area, it is necessary to start at low speed from the start area and then accelerate. When stopping, you need to act in the reverse order: first perform braking, and only after entering the start area can you stop supplying control pulses.
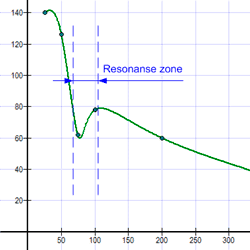
Stepper motor resonance
Stepper motors have an undesirable effect called resonance. The effect shows itself as a more noisy operation, more vibration and sudden drop in torque at some speeds. This can lead to missed steps and loss of synchronicity. The effect appears if the step frequency coincides with the natural resonant frequency of the stepper motor rotor.