Stepper motors have an undesirable effect called resonance. The effect shows itself as a more noisy operation, more vibration and sudden drop in torque at some speeds. This can lead to missed steps and loss of synchronicity. The effect appears if the step frequency coincides with the natural resonant frequency of the stepper motor rotor.
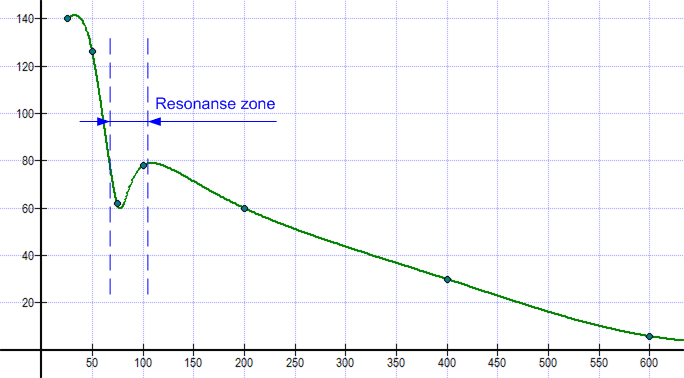
When the motor moves a step, the rotor does not immediately move to a new position, but performs damped oscillations. The fact is that the rotor - magnetic field - stator system can be considered as a spring pendulum, the frequency of oscillations of which depends on the rotor and load inertia and the magnitude of the magnetic field. Due to the complex configuration of the magnetic field, the resonant frequency of the rotor depends on the amplitude of the oscillations. As the amplitude decreases, the frequency increases, approaching the low‑amplitude frequency, which is more easily calculated quantitatively. This frequency depends on the step angle and on the ratio of the holding torque to the moment of inertia of the rotor. A larger holding torque and a smaller moment of inertia lead to an increase in the resonant frequency.
The resonant frequency is calculated using the formula:
F0 = (N ∙ TH / (JR+JL))0.5 / (4 ∙ pi),
F0 – resonant frequency,
N – number of full steps per revolution,
TH – holding torque for the used control method and phase current,
JR – rotor moment of inertia,
JL – load moment of inertia.
It should be noted that the resonant frequency is determined by the moment of inertia of the motor rotor itself plus the moment of inertia of the load connected to the motor shaft. Therefore, the resonant frequency of the rotor of an unloaded motor, which is sometimes given among the parameters, has little practical value, since any load connected to the motor will change this frequency.
In practice, the resonance effect leads to difficulties when operating at frequencies close to the resonant one. The torque at the resonance frequency is zero, and without taking special measures, the stepper motor cannot pass the resonant frequency during acceleration. In any case, the phenomenon of resonance can significantly degrade the precision characteristics of the drive.
Low damping systems run the risk of losing steps or increasing noise when the motor operates near its resonant frequency. In some cases, problems may also arise at harmonics of the fundamental resonance frequency.
When a non‑microstepping mode is used, the main cause of oscillation is intermittent rotation of the rotor. When taking a step, some energy is imparted to the rotor by a push. This push excites vibrations. The energy supplied to the rotor in half‑step mode is about 30% of the energy of a full step. Therefore, in the half‑step mode, the oscillation amplitude is significantly smaller. In microstepping mode with a step of 1/32 of the main one, only about 0.1% of the energy of the full step is reported for each microstep. Therefore, in microstepping mode, the phenomenon of resonance is practically unnoticeable.
Various methods can be used against the resonance phenomenon. For example, the use of elastic materials when making mechanical couplings with a load. The elastic material promotes the absorption of energy in the resonant system, which leads to the attenuation of parasitic oscillations.
Another way is to use viscous friction. Special dampers are used. These dampers have a metal disc, which can rotate inside a hollow cylinder filled with a viscous silicone lubricant. When this system rotates with acceleration, the disk experiences viscous friction, which effectively dampens the system.
There are also electrical methods against the resonance phenomenon. An oscillating rotor leads to the appearance of an EMF in the stator windings. Shorting windings that are not being used in this step will dampen the resonance.
And finally, there are methods against the resonance phenomenon at the level of the stepper motor driver operating algorithm. For example, use the fact that when working with two phases on, the resonant frequency is approximately 20% higher than with one phase on. If the resonant frequency is precisely known, then it can be passed by changing the operating mode.
If possible, frequencies higher than resonant should be used when starting and stopping. Increasing the moment of inertia of the rotor‑load system reduces the resonant frequency.
The most effective way against the resonance is using microstepping mode.