Strictly speaking, it is more correct to say that it is not the stepper motor itself that is bipolar or unipolar, but its connection to the control driver. Some motors have one winding in each phase, which must be reversed by the driver to change the direction of the magnetic field. This type of motor requires a bridge driver, or a half‑bridge driver with bipolar power supply. In total, such a motor has two windings and, accordingly, four terminals and therefore allows only one connection option - bipolar. This type of motor can be called a bipolar stepper motor.
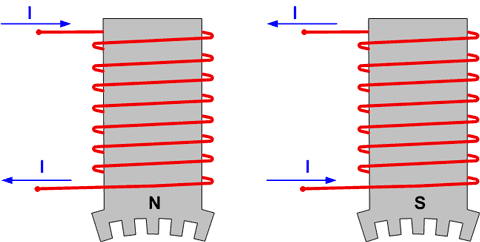
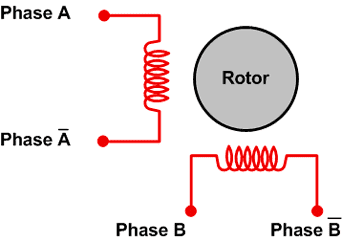
A unipolar stepper motor also has one winding in each phase, but a tap is made from the middle of the winding. This allows to change the direction of the magnetic field created by the winding by simply switching the winding halves. At the same time, the driver circuit is significantly simplified. The driver should only have 4 simple keys. So, a unipolar motor uses a different method of changing the direction of the magnetic field. The middle terminals of the windings can be combined inside the motor, so such a motor can have 5 or 6 terminals.
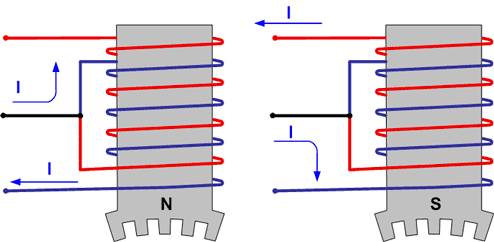
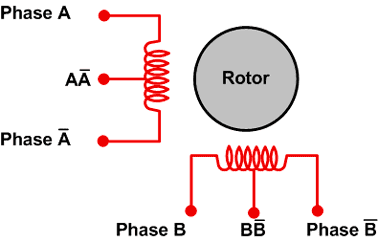
Sometimes stepper motors have 4 separate windings. Each winding has separate terminals, so there are 8 terminals in total. With appropriate winding connections, such a motor can be used as unipolar or bipolar. A unipolar motor with two windings and taps can also be used in bipolar mode if the taps or phase ends are left unconnected.
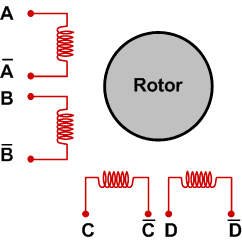
The torque produced by a stepper motor is proportional to the magnitude of the magnetic field created by the stator windings. The way to increase the magnetic field is to increase the current or the number of turns of the windings. A natural limitation when increasing winding current is the danger of saturation of the iron core. However, in practice this restriction rarely applies. Much more significant is the limitation on motor heating due to ohmic losses in the windings. This fact demonstrates one of the advantages of bipolar connection of stepper motors. With a unipolar motor connection, only half of the windings are used at any given time. The other half simply takes up space in the core window, which forces the windings to be made with smaller diameter wire. At the same time, with a bipolar motor connection all windings are always in use and work optimal. In such stepper motors, the cross‑section of every windings is twice as large, and the ohmic resistance is correspondingly half as large. This allows to increase the current to the root of two times with the same losses, which gives a gain in torque of approximately 40%. If increased torque is not required, a unipolar motor connection allows to reduce dimensions or simply operate with lower losses. Unipolar motors are still used, because they require much simpler winding control circuits.