The full‑step operating mode of a stepper motor can be implemented in two ways.
The first control method is provided by alternating phase switching. Phases switching do not overlap - only one phase is turned on at one time. This method is called «one phase on» full step or wave drive mode. The rotor equilibrium points for each step coincide with the «natural» rotor equilibrium points of an unpowered motor. The disadvantage of this control method is that only 50% of the windings are used at the same time for a bipolar connection, and only 25% for a unipolar motor connection. This means that the full torque cannot be obtained in this mode.

The second method is with phase overlap control: two phases are switched on at the same time. It is called «two‑phase‑on» full step or simply full step mode. The rotor is fixed in intermediate positions between the stator poles with this control method. And approximately 40% more torque is provided than in the case of one phase on. This control method provides the same step angle as the first method, but the position of the rotor balance points is shifted by half a step.
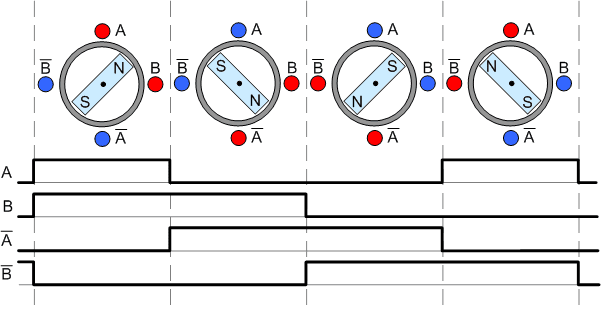
The positions of the rotor equilibrium points are shifted by half a step in full‑step mode with two phases turned on. It should be noted that the rotor takes these positions when the motor is running, but the position of the rotor cannot remain unchanged after the winding current is turned off. Therefore, when turning the motor power on and off, the rotor will move half a step. To prevent it from shifting when stopped, it is necessary to supply a holding current to the windings. The same is true for half‑stepping and microstepping modes. It should be noted that if the motor rotor was turning when the motor was turned off, then when the power was turned on, the rotor could shift by more than half a step.
The holding current may be less than the rated current, since a motor with a fixed rotor usually does not require much torque. However, there are applications where the motor must provide full torque when stopped, which is possible for a stepper motor. This property of the stepper motor allows in such situations to do without mechanical braking systems. Since modern stepper motor drivers allow to regulate the supply current to the motor windings, setting the required holding current is usually not a problem. The task is usually simply to provide appropriate software support for the control microcontroller.