Most controllers at the industrial market offer one input signal option for DC motor speed control. Most often, this is an analog voltage signal with a fixed range. Such devices fit well into existing systems only if the control device has the ability to generate the appropriate signal. The new controller BMD‑20DIN ver.2 offers 6 different signal options for motor speed regulation, so its compatibility and ability to use with various devices is significantly wider.
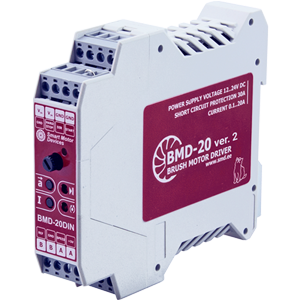
DC Motor speed control
In order to expand the applications range, 6 different ways to control DC motor speed is the BMD‑20DIN ver.2 controllers are provided:
- analog voltage signal 0...5 VDC;
- analog voltage signal -10...+10 VDC;
- analog signal 4...20 mA (current loop);
- PWM regulation;
- internal built-in potentiometer;
- external potentiometer.
Functions and features:
To successfully integrate the drive into the system, the controller must provide full functionality for motor control. The more functions the drive itself can implement, the fewer add-ons and functions will be required from an external control controller. Based on these considerations, we have added to the controller all the necessary functionality for controlling the motor in speed control mode and equipped the device with the necessary protection functions.
Controllers BMD‑20DIN ver.2 ensure successful operation of the drive in the system due to full functional of DC motor control. The rotation speed is controlled using a built-in regulator or an external analog signal. The device provides start/stop and change of direction of rotation using discrete signals, and also provides the ability to adjust soft start and deceleration. The operating logic of discrete control signals is easily customizable by a user - triggering on low/high levels or on the edge of a signal is selected using jumpers.
The controller has a HARD STOP signal that can be used to organize a safety loop. When such a circuit with the HARD STOP signal is opened, the controller turns off the motor.
To protect the motor from overload, and the mechanics from excess torque, the motor current limiting function is used - a user has the ability to set the maximum operating current in the range from 0.2 A to 20 A.
The controller is equipped with protection against short circuit, overheating and exceeding the input voltage range. Such protection features are necessary to ensure the reliability of the device, which is usually not found in low-quality controllers.
Final result
As a result of the efforts of Smart Motor Devices engineers, a cost-effective, full-featured and reliable controller BMD‑20DIN ver.2 for DC brush motors is available now at the industrial market.