Specialists of Smart Motor Devices continuously monitor trends and needs of the modern industrial market. Taking into account the experience with existing models of the company, as well as the wishes and requirements of users for new devices, our engineers have developed a new unit to control torque and speed of DC brush motors. The new controller BMD‑40DIN ver.2 includes all the advantages and capabilities of the previous model BMD‑20DIN ver.2, and also has new functionality.
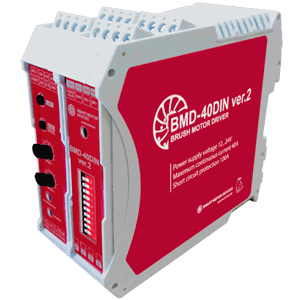
DC Motor speed and torque control
According to statistics, brush DC motors are one of the most common drive options for electromechanical devices. And most of these drives require high-quality and stable speed control. However, a significant part of applications also use these drives to operate with controlled torque on the output shaft. Therefore, the new controller model BMD‑40DIN ver.2 is designed to control the speed and torque of DC motors.
To be able to integrate the controller into any system, the controller provides 7 different ways to control speed and torque of a DC motor:
- analog voltage signal 0...5 VDC;
- analog voltage signal 0...10 VDC;
- analog voltage signal -10...+10 VDC;
- analog signal 4...20 mA (current loop);
- PWM regulation;
- internal built-in potentiometer;
- external potentiometer.
Stop control signal zones prevent shaft drift at zero speed setpoint
To prevent drift of the motor shaft under the influence of interferences on the control lines, we have provided dead zones - zones of insensitivity of the controller to the analog voltage input signal (0V to 1% of max. voltage level of the signal). This makes it possible to use the drive in noisy environments or when using an imprecise or unstable signal source.
«Second speed» function
There are tasks when it is necessary to switch to another value of a given speed temporarily, and then return to regulation with an analog signal. For such tasks, we have provided the function “second speed” - the speed value is set by the built-in potentiometer, and speed switching is performed by an external discrete signal. The function is convenient for fast movements at idle speed, searching for the home position, returning to preset positions, etc.
Discrete I/O signals
In order to make it possible to successfully integrate the drives into technical systems, the controller has configurable input and output signals:
DIR – the input signal is used to control motor rotation direction. The input logic can be adjusted to operate according a level of the signal or according to a falling edge of the signal.
START/STOP – the input signal is used to start and stop the motor. The input logic can be adjusted to operate according a level of the signal or according to a falling edge of the signal.
SECOND SPEED – the input signal is used to switch to the second given speed.
BRAKE – the input is used to control the motor holding brake (connected to the output BR+/BR-). The active signal level can be adjusted to either low or high levels.
HARD_STOP – the input signal is used to create an emergency circuit. The controller turns off the motor if the signal is triggered. The logic of the signal can be configured to trigger on closed or open circuit.
FLT – the output signal is used to control the operation state of the drive, an external control device can monitor errors or alarms of the drive using this output.
BR+/BR- – this output is used to supply power to the motor holding brake. This output is controlled by a configurable BRAKE input signal.
Motor current limiting function
As in previous models, the controllers BMD‑40DIN ver.2 provide a function for limiting the motor current. This function protects the motor from over-current and, as a result, ensures that the output torque on the shaft does not exceed the permitted value, thereby ensuring the mechanical safety of the equipment.
The range of setting the allowed current has been expanded to 1A to 40A. If the set value is exceeded for more than 5 seconds, the controller turns off the motor and goes into HARD_STOP mode.
Protection
The controller is equipped with protection against short circuit, overheating and exceeding the input voltage range. Such protection features are necessary to ensure the reliability of the device, which is usually not found in low-quality controllers.
Conclusion
As a result of a thorough study of market needs and the high-quality work of Smart Motor Devices engineers, a new universal and reliable controller BMD‑40DIN ver.2 has become available to developers of technical equipment and industrial systems.