DC brushless motor controllers
BLDC motor controllers for speed and position control of 3-phase DC brushless motors with Hall sensors. Two series BLD and BLSD are intended for BLDC control 24V - 48V motors power up to 1000 W power.
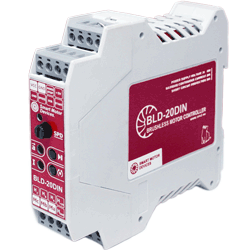
BLD‑20DIN
Brushless DC motor controller
Voltage
24 – 48 VDC
Rated current
up to 20 A
Peak current
30 A
Control methods
Analog input
The driver is designed to control 3-phase DC motors with Hall sensors. It is suitable for small and medium size motors with current under 20 A. This model provides analog speed control, acceleration and deceleration regulation. Adjustable current limitation prevents motor overload and damage. Digital inputs START/STOP, DIR, HARD STOP are useful for system integration.
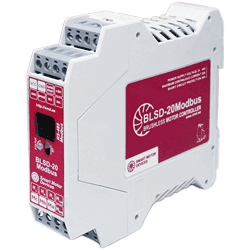
BLSD‑20Modbus
Brushless DC motor controller
Voltage
24 – 48 VDC
Rated current
up to 20 A
Peak current
30 A
Control methods
RS-485 Modbus (speed or position), analog input, program
The controller is designed to control 3-phase BLDC motors with Hall sensors. The model provides RS-485 Modbus ASCII/RTU communication for programming, setting of operation parameters and state control. BLSD‑20Modbus provides speed and position control, motor current limitation, holding possibility. The controllers have active braking capability and provide four-quadrant control of a DC brushless motor.
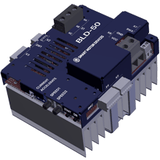
BLD-50
Brushless DC motor controller
Voltage
12 – 48 VDC
Rated current
up to 50 A
Peak current
100 A
Control methods
Analog speed control 0...5 V, 0 … 10 V, -10...10 V, 4...20 mA, PWM
The controller BLD-50 is designed to control 3-phase brushless motors with Hall sensors. Maximum current of up to 50 A is suitable for medium and big size motors. The controller provides current limiting function, four-quadrant phase control, control of motor brake. Also there are second-speed function and possibility to connect an external braking resistor.
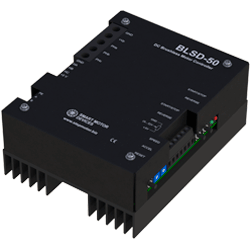
BLSD‑50
Brushless DC motor controller
Voltage
24 – 48 VDC
Rated current
up to 50 A
Peak current
60 A
Control methods
Analog input, RS‑485
BLSD‑50 is a controller for DC brushless motors with Hall sensors with communication interface RS‑485. The controller is designed for medium and big size brushless motors with current under 50 A. It provides motion control by input signals or by commands via RS‑485.
About DC brushless motor controllers
A brushless DC motor with Hall sensors is a sophisticated system that combines the advantages of BLDC technology with precise speed control. These drives rely on Hall effect sensors to provide feedback regarding the position of the rotor magnets. This information is then used by the controller to regulate the motor's speed and direction of rotation.
The controller for a BLDC motor consists of several essential parts. The primary component is the brushless motor driver. Its role is to receive control signals and convert them into electrical pulses that drive the motor's phases. The brushless driver ensures the motor operates in perfect synchronization with the desired speed and direction.
To achieve accurate speed control, a brushless motor speed controller is employed. This component utilizes the feedback from the Hall effect sensors to detect the position of the rotor relative to the stator. Based on this feedback, the controller adjusts the phase currents, enabling precise speed control. The brushless motor speed controller is responsible for maintaining the desired speed and adapting to changes in load or operating conditions.
The electrical circuit of a brushless motor controller includes various features to optimize performance and protect the motor and the controller itself. Power electronics, such as transistors or MOSFETs, are crucial elements of the circuit. These devices switch the current flow to the motor's phases, controlled by a microprocessor or digital signal processor (DSP) within the controller. The microprocessor executes control algorithms that determine the timing and amplitude of the phase currents based on the feedback received from the Hall sensors.
In addition to the control circuitry, the brushless motor controller's electrical circuit incorporates protective features. These safeguards include overcurrent protection and overtemperature protection, which monitor the motor's operating conditions and take appropriate actions to prevent damage. For instance, the controller might reduce the current or trigger an alarm if critical limits are exceeded.
For example, the 48V brushless motor controller is designed to work with motors powered by a 24-48V power supply . This controller provides efficient power conversion and control for applications requiring higher voltage levels. It integrates seamlessly with the motor and ensures optimal performance and compatibility.
Another option is the electronic speed controller (ESC), which combines all the necessary components, including the brushless motor driver, speed controller, and additional control features, into a single unit. The ESC simplifies the wiring and setup process, offering a compact and user-friendly solution for controlling brushless DC motors. It often includes programmable parameters, braking capabilities, and motor protection mechanisms.
In summary, brushless DC motors with Hall sensors offer precise speed control through the utilization of a brushless motor driver and a brushless motor speed controller. The controller's electrical circuit comprises power electronics, a microprocessor or DSP, and protective features. A 48V brushless motor controller is specifically designed for motors operating at 48V, while a brushless electronic speed controller consolidates all the necessary components into a single unit for easy integration and efficient control of the motor.