DC brush motor controllers
Our models BMD and BMSD series provide 12V and 24V motor speed control for DC brush motors up to 40A rated current. Our controllers also provide position control for models with encoder.
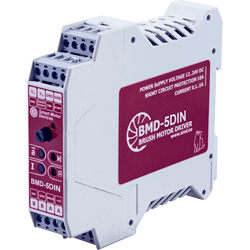
BMD‑5DIN
DC brush motor speed controller
Voltage
12 – 24 VDC
Rated current
up to 5 A
Peak current
10 A
Control methods
Analog speed control 0...5 V or 0...10 V
BMD‑5DIN is a speed controller for small size DC brush motors. The controller is cheaper than the base 20A version, but it can be used in the most standard low and medium power systems. Motor speed is regulated by 0...5 or 0...10 VDC analog signal or can be adjusted by an internal potentiometer. Acceleration and deceleration time are also adjusted by potentiometers.
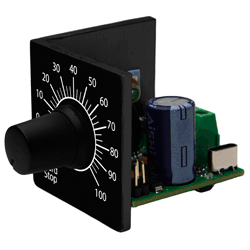
BMD‑12
Built-in DC brush motor speed controller
Voltage
12 – 24 VDC
Rated current
up to 12 A
Speed stabilization method
BEMF
Control methods
Speed control (potentiometer or via PC)
BMD‑12 is a built-in speed controller for DC brush motors. The controller provides load compensation and stabilization of rotation speed without an encoder based on the back EMF of the motor. BMD‑12 is equipped with a fully-featured PID controller. Independent settings for PID coefficients allow achieving ideal drive operation for any operating speeds and loads.
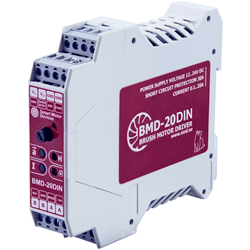
BMD‑20DIN
Brush DC motor controller
Voltage
12 – 24 VDC
Rated current
up to 20 A
Peak current
30 A
Control methods
Analog speed control 0...5 V
BMD‑20DIN is a speed driver for DC brush motor. Motor speed is regulated by 0...5 VDC analog signal or can be adjusted by an internal potentiometer. Acceleration and deceleration time are also adjusted by potentiometers. The controller provides current limitation function to prevent motor overloading.
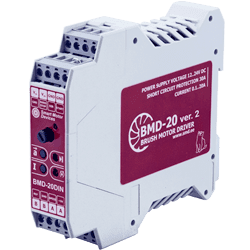
BMD‑20DIN ver.2
Brush DC motor controller
Voltage
12 – 24 VDC
Rated current
up to 20 A
Peak current
30 A
Control methods
Analog speed control 0...5 V, -10...10 V, 4...20 mA, PWM
BMD‑20DIN ver.2 is a DC brush motor speed controller. The controller provides different methods of motor speed regulation, using potentiometers, analog or PWM signal. Acceleration and deceleration time are also adjustable. This motor speed controller provides current limitation function to prevent motor overloading.
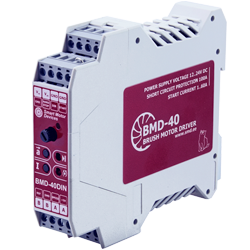
BMD‑40DIN
Brush DC motor controller
Voltage
12 – 24 VDC
Rated current
up to 40 A
Peak current
100 A
Control methods
Analog speed control 0...5 V
BMD‑40DIN is a driver for DC brush motor, which is used for speed, acceleration and deceleration control. Regulation methods: analog signal 0...5 VDC analog signal or internal potentiometer. Current limitation function prevents motor overloading.
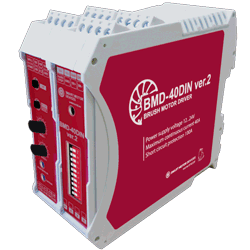
BMD‑40DIN ver.2
Brush DC motor controller
Voltage
12 – 24 VDC
Rated current
up to 40 A
Peak current
100 A
Control methods
Analog speed and torque control 0...10 V, -10...10 V, 4...20 mA, PWM
BMD‑40DIN ver.2 is a driver designed to control torque, speed, direction, acceleration and deceleration of a DC brush. There are current limiting and second speed functions.
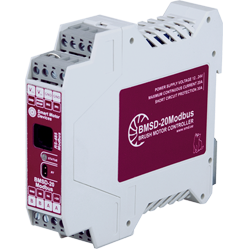
BMSD‑20Modbus
Brush DC motor controller
Voltage
12 – 24 VDC
Rated current
up to 20 A
Peak current
30 A
Control methods
RS-485 Modbus (speed or position), Pre‑programmed motion
BMSD‑20Modbus is a programmable controller for DC brush motors. The unit can be controlled via RS-485 Modbus ASCII or RTU. It provides speed and position control (for motors with encoder). There are programmable digital inputs. Adjustable current limitation function is provided.
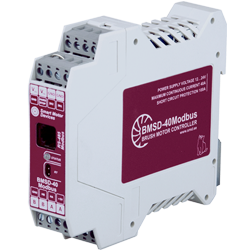
BMSD‑40Modbus
Brush DC motor controller
Voltage
12 – 24 VDC
Rated current
up to 40 A
Peak current
100 A
Control methods
RS-485 Modbus (speed or position), Pre‑programmed motion
BMSD‑40Modbus is a programmable controller for DC brush motors. The unit can be controlled via RS-485 Modbus ASCII or RTU. It provides speed and position control (for motors with encoder). There are programmable digital inputs. Adjustable current limitation function is provided.
About DC brush motor controllers
DC brush motors are a type of electric motors that utilize brushes and a commutator for the conversion of electrical energy into mechanical energy. These motors are commonly used in various applications due to their simplicity and cost-effectiveness. Control of DC motor speed requires a DC motor controller, which consists of several essential parts and features in its electrical circuit.
The electrical circuit of a controller typically includes power transistors or MOSFETs. These devices act as switches, controlling the flow of current to the motor's armature windings. The motor driver uses pulse-width modulation (PWM) techniques to vary the duty cycle of the control signals, effectively adjusting the average voltage applied to the motor. This modulation technique allows for precise speed control of the DC brush motor.
Another critical part such controller is the speed control mechanism. This mechanism varies the speed setpoint of the motor, allowing the user to adjust the desired speed. It can be implemented using various methods, such as potentiometer, analog or digital interface, or a closed-loop control system with feedback sensors. The speed control mechanism provides the flexibility to match the motor's speed to the specific requirements of the application.
Additionally, the electrical circuit may incorporate protective features to ensure safe operation and prevent damage to the motor. These protective features include overcurrent protection, overvoltage protection, and thermal protection. They monitor the motor's operating conditions and take appropriate actions, such as reducing the current or shutting down the system, to prevent overheating or overloading.
Furthermore, some advanced DC brush motor controllers may include additional features to enhance performance and functionality. These features can include dynamic braking, which provides rapid deceleration of the motor, and current limiting, which prevents excessive current draw during high-load conditions. Some controllers also offer regenerative braking, allowing the motor to act as a generator and convert kinetic energy into electrical energy during braking.
In conclusion, control of the of a DC motor speed requires a DC motor controller with specific parts and features in its electrical circuit. The motor driver, power transistors, and PWM techniques allow for precise speed control. The speed control mechanism provides adjustability of the motor's speed, while protective features ensure safe operation. Advanced features like dynamic braking and current limiting further enhance the controller's performance. Overall, a well-designed DC motor controller provides efficient and reliable speed management for DC brush motors in various applications.