Built-in DC brush motor speed controller BMD‑12
Voltage
12 – 24 VDC
Rated current
up to 12 A
Speed stabilization method
BEMF
Control methods
Speed control (potentiometer or via PC)
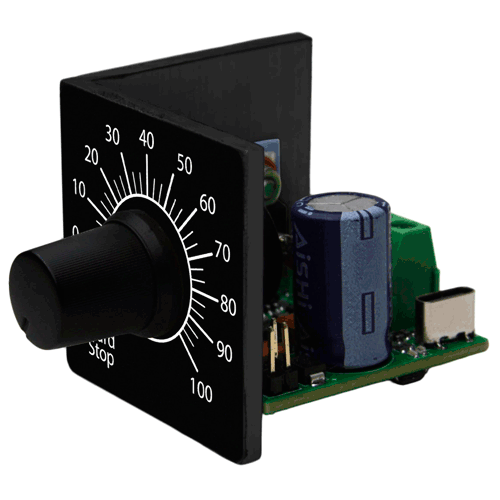
BMD‑12 is a built-in speed controller for DC brush motors. The controller provides load compensation and stabilization of rotation speed without an encoder based on the back EMF of the motor. BMD‑12 is equipped with a fully-featured PID controller. Independent settings for PID coefficients allow achieving ideal drive operation for any operating speeds and loads.
Technical data
Operating voltage
12 – 24 VDC
Current limit adjustment range
0.5 – 12 A
Short circuit protection (external fuse not required)
5.5 – 17 А, 55 μs
Motor power
up to 300 W
Motor PWM frequency
18 kHz
Communication interface
USB
Operating voltage
12 – 24 VDC
Current limit adjustment range
0.5 – 12 A
Short circuit protection (external fuse not required)
5.5 – 17 А, 55 μs
Motor power
up to 300 W
Motor PWM frequency
18 kHz
Communication interface
USB
Dimensions and installation of built-in DC brush motor controller BMD‑12
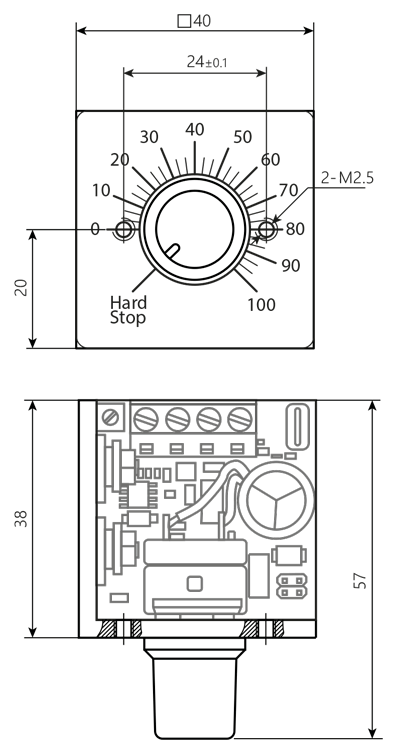
Description of built-in DC brush motor controller BMD‑12
BMD‑12 is designed for speed control and stabilization of a motor without encoder. Adjustable current limit provides overload protection.
BMD‑12 is made as an electronic device without a case and is intended for embedding into a panel. The device is convenient to use for operator control panels of various devices.
Speed control modes:
- speed control by a potentiometer without stabilization;
- speed control by a potentiometer and speed stabilization by back EMF;
- setting the speed by parameters via USB without stabilization;
- setting the speed by parameters via USB, with speed stabilization.
It is possible to set the target motor speed either by a potentiometer knob or through a software (connection to a PC via USB).
Load compensation and speed stabilization
The compensation function allows stabilizing the motor speed regardless of the load on the motor shaft. An external encoder on the motor is not required, the speed is stabilized by using the back EMF measured during motor rotation.
Motor overload protection
The controllers BMD‑12 have adjustable motor overload protection. The user can set the required maximum motor current value up to 12A. The function can be used both to protect the motor from current overload and to protect the mechanics from exceeding the permissible torque.
Software setting of operating parameters
Operation parameters can be controlled and adjusted via USB. The software is provided with the device. The software allows to adjust the control mode, target speed and target back EMF values, acceleration and braking ratio, and also to configure the PID parameters for the speed stabilization mode.
Full-fledged PID regulator
The requirements for the accuracy of maintaining motor velocity and speed of stabilization depend on the specific task and can vary greatly. Different motor models have different characteristics and react differently to changes in load and speed compensation. In addition, the nature of the load itself can have different parameters (inertia, cyclicity, change in value over time).
In order to adapt any motor models to tasks with high requirements for speed maintenance accuracy and to configure them for operation with a changing load, the controllers BMD‑12 have a full-fledged PID controller. The coefficients the PID are available for editing by customer.
Changing the proportional coefficient allows to adjust the drive's response time to changes in load and speed and reduce the magnitude of the constant error. The integral coefficient allows to reduce the steady-state speed error to zero, and the differential component eliminates system oscillations. Thus, a controller with a PID regulator allows to achieve smooth operation of the drive at a constant speed, without jerks when the load at the motor shaft changes.
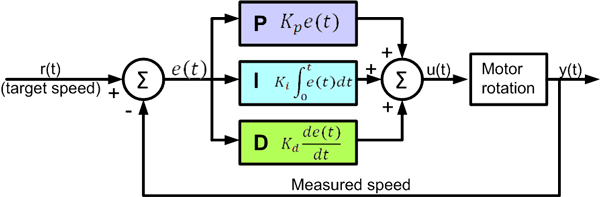
Load compensation and speed stabilization based on motor back EMF
The controllers BMD‑12 implement rotation speed stabilization based on the back EMF of the motor, since this method is optimal both in terms of the cost of the final system and in terms of the motor performance.
It is known that the rotation speed of a DC brush motor depends on the load torque. To stabilize the speed when the load changes, an external controller and a feedback system are required to detect the change, correct the control action and stabilize the rotation speed
There are several feedback options that can be used to solve the speed stabilization task: current feedback, external encoder feedback, and motor back EMF feedback.
Speed stabilization based on the motor's back EMF is the best option for industrial systems using a motor without an encoder. On the one hand, the system is budget-friendly (unlike encoder based devices), since it can be used with a motor without an encoder. On the other hand, there is no need for initial setup, as in the case of current feedback. When stabilizing speed based on BEMF, the controller monitors the motor speed, the correction is faster, and when the load changes, there are no jerks or self-oscillations (unlike load compensation RxI based devices), typical for devices with current feedback.
Read more in our press-release
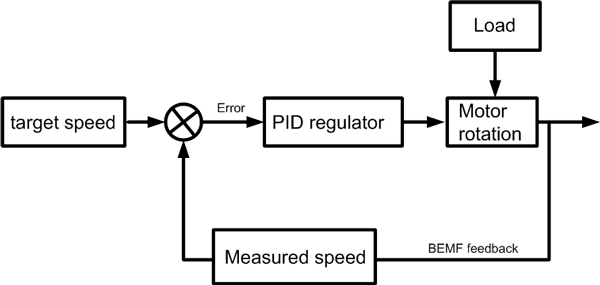
Wiring diagram and control elements layout
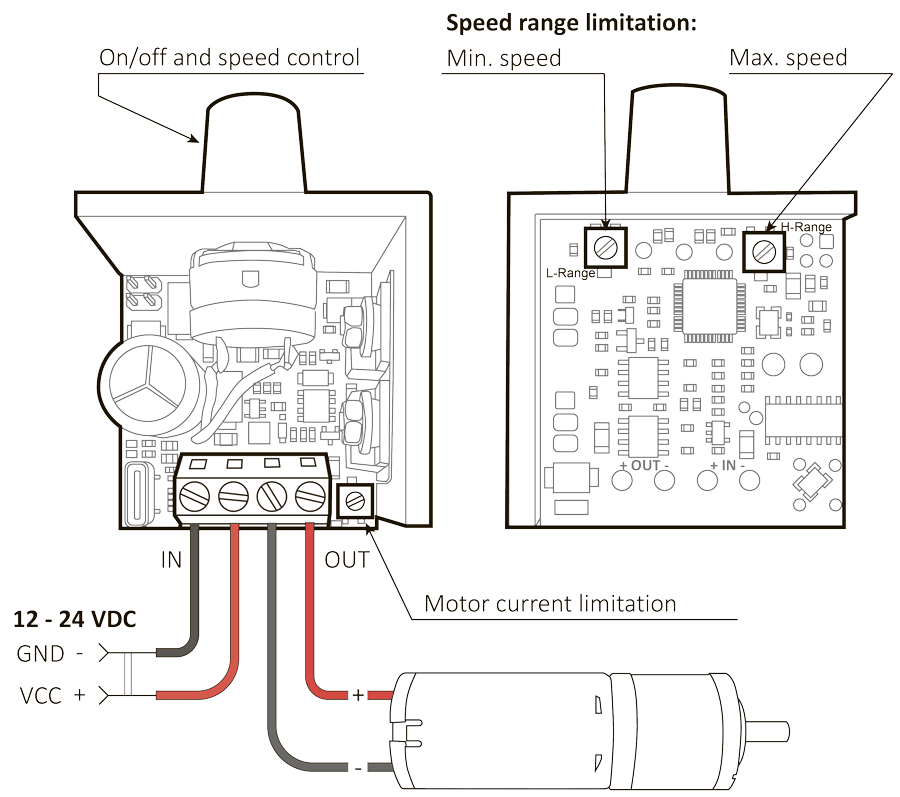
Software and parameterization of the controller BMD‑12
The BMD-control-mini program is designed for quick initial parameterization of the controllers BMD‑12, as well as for performing test movements - setting speed and acceleration, starting and stopping the DC motor.
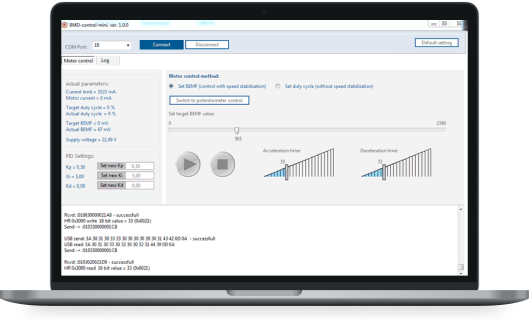
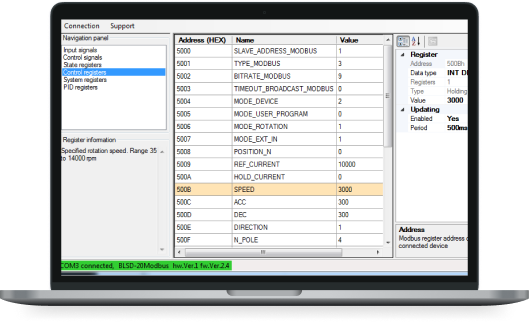
The controller operation can be fine configured using registers, which can be changed via USB connection. The software Modbus Basic Utility is designed to access all settings and registers of the controller. Using the Modbus Basic Utility, you can perform precise adjustment of the drive for systems with high requirements for the accuracy of maintaining speed for any load options and different DC motor models.
Get a quote
Dear guest
Thanks for your message!
We will contact you as soon as possible.
Error
Something goes wrong.
Please try later.