DC brush motors are usually characterized by low cost, simple design and ease of operation. These characteristics allow such motors to remain budget and one of the most common types of electric drives. However, the known disadvantages of DC brush motors (short service life due to high starting currents and dependence of speed on load) limit their capabilities and areas of application. To eliminate these disadvantages and preserve the advantages of this motor type, Smart Motor Devices developed a new device - a DC brush motor controller BMD‑12 with a speed stabilization function, adjustable soft start and stop, with a motor current limitation function. BMD‑12 is a full‑fledged PID controller and allows compensating for load variations and speeding fluctuations unlike devices based on load compensation RxI.
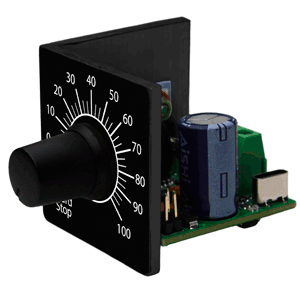
BMD‑12 provides:
- DC brush motor speed control;
- load compensation and motor speed stabilization without an encoder;
- adjustable smooth motor start and stop;
- a full‑fledged PID regulator to achieve ideal operation of any engine and load options.
Load compensation and speed stabilization based on motor back EMF
The controllers BMD‑12 implement rotation speed stabilization based on the back EMF of the motor, since this method is optimal both in terms of the cost of the final system and in terms of the motor performance.
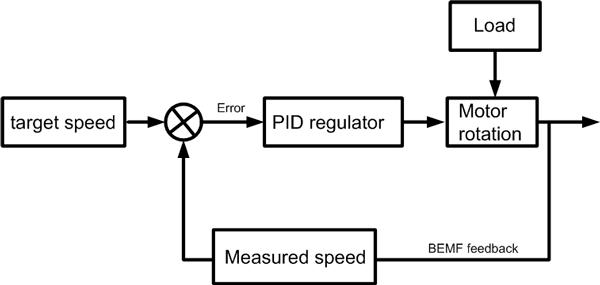
It is known that the rotation speed of a DC brush motor depends on the load torque. To stabilize the speed when the load changes, an external controller and a feedback system are required to detect the change, correct the control action and stabilize the rotation speed.
There are several feedback options that can be used to solve the speed stabilization task: current feedback, external encoder feedback, and motor back EMF feedback.
1. Data from an encoder (resolver, tachogenerator) is often used as a feedback source. An external encoder is mounted directly on a motor. Data from the encoder is processed by the external controller processor, the calculated speed error is compensated by changing the control action. However, this approach, while eliminating one problem - speed fluctuations when changing the load, adds another - complicating and increasing cost of the system. Therefore, feedback based on data from the encoder is more suitable and is used in systems where positioning is required or information about the current position of the shaft is needed.
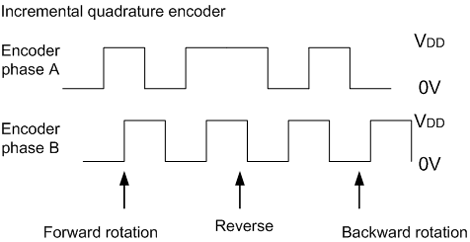
2. Current feedback is often used in budget systems where output speed must be approximately maintained, but there are no strict requirements for the actual speed and drive response time to load changes. Typical examples of devices based on load compensation RxI controllers are household sewing machines, home power tools (drills, screwdrivers), kitchen appliances (mixers, meat grinders, etc.). The control principle itself is based on monitoring load changes, and speed stabilization is performed secondarily. Due to the oscillatory processes of such a system, speed stabilization is carried out with a delay, jerks and twitches are inevitable when the load changes. Another significant drawback of such devices is the need for manual adjustment of each device with a specific motor. During the adjustment, not only speed adjustment is required, but also imitation of the motor load. In this case, the compensation level is selected empirically (usually manually using a potentiometer knob or a trimmer resistor) based on the test load results. If during operation the operating speed or load differs significantly from the test ones, the quality of speed stabilization will be worse.
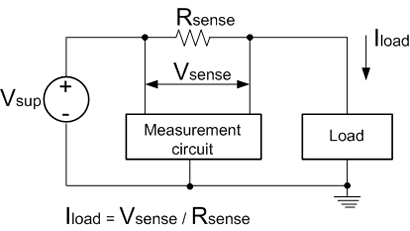
3. Speed stabilization based on the motor's back EMF is the best option for industrial systems using a motor without an encoder. On the one hand, the system is budget‑friendly (unlike encoder based devices), since it can be used with a motor without an encoder. On the other hand, there is no need for initial setup, as in the case of current feedback. When stabilizing speed based on BEMF, the controller monitors the motor speed, the correction is faster, and when the load changes, there are no jerks or self‑oscillations (unlike load compensation RxI based devices), typical for devices with current feedback.
Full‑fledged PID regulator
The requirements for the accuracy of maintaining motor velocity and speed of stabilization depend on the specific task and can vary greatly. Different motor models have different characteristics and react differently to changes in load and speed compensation. In addition, the nature of the load itself can have different parameters (inertia, cyclicity, change in value over time).
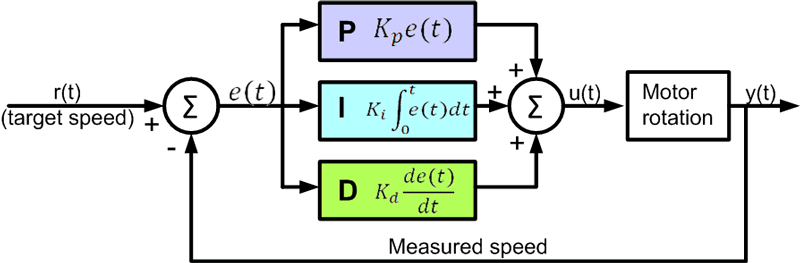
In order to adapt any motor models to tasks with high requirements for speed maintenance accuracy and to configure them for operation with a changing load, the controllers BMD‑12 have a full‑fledged PID controller. The coefficients the PID are available for editing by customer.
Changing the proportional coefficient allows to adjust the drive's response time to changes in load and speed and reduce the magnitude of the constant error. The integral coefficient allows to reduce the steady‑state speed error to zero, and the differential component eliminates system oscillations. Thus, a controller with a PID regulator allows to achieve smooth operation of the drive at a constant speed, without jerks when the load at the motor shaft changes.